皆さん、生産に使用する設備導入って対応されたことはあるでしょうか?
私は製造技術系の技術者ですが、これまで人が少ないという理由で設備導入にも携わってきました。初めて設備導入を担当したときは、製造対応とは勝手が全く異なり正直非常に苦労しました。
今回は、はじめて設備導入をされる方向けとして基本的な流れについて解説したいと思います。
ところで、設備導入は技術部門の中ではどういった括りになるのでしょうか?私なりの認識は以下の通りです。会社によっては人員が少ないと両方兼務もあるのかなと思います。
<技術部門>
- 製造技術:プロセス設計、プロセス改善
- 生産技術:設備導入、設備保全
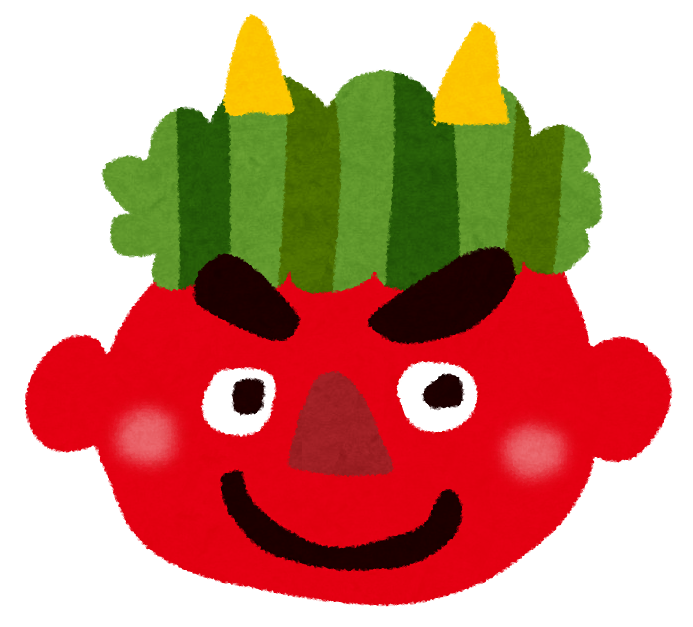
それでは、基本の流れについて解説させていただきます。
基本の流れは以下の通りです。
- コンセプト決定
- 基本設計
- 詳細設計
- 決済・施工
- 検収・稼働
- バリデーション※
※バリデーションは、1~5の流れと並行して実施するものですのでご注意下さい!
コンセプト決定
どのような設備を入れるのかを決めます。新規導入 or 更新なのか、おおよその設備仕様、予算規模はどれぐらいなのかを決定します。
決定する項目は以下の通りです。
- コンセプト:自動化、省人化、IOTの程度をどの程度にするのか?
- 設備能力:時間当たりの生産能力、年間の生産量も含めてどの程度にするか?
- 必要人員:設備を稼働させるために必要な人員はどの程度か?
- 予算:どれぐらいの予算規模にするのか?(数百万円~数億円)
- スケジュール:どれくらいの時期に導入するか?
導入する設備の大枠をあくまでも概算になりますがここで決定します!
基本設計
次に基本設計です。→実はここがめちゃくちゃ大事です!
このフェーズからは、いくつかの設備を同時に導入する場合はエンジニアリング会社に依頼することが多いです。設備単体であれば、エンジニアリング会社を使用しない場合もあります。尚、エンジニアリング会社に依頼すると楽な反面、費用が+αで必要になります。
このフェーズで実施することは以下の通りです。
- エンジニアリング会社の選定(必要に応じて)
- コンセプト決定(コンセプト、設備能力、必要人員、予算、スケジュール)
- 要求仕様の決定(こちらが求める設備の仕様を決める)
- 生産設備メーカーの選定(2~5社程度)
- メーカーへの概算見積依頼
- 概算見積書取得(見積書、見積仕様書)
設備メーカーは単独一社だけで進めるということはほとんどなく、2~5社から相見積を取得することになります。あまりたくさんのメーカーを選定するのは現実的ではないです。対応する人員にもよりますが、MAXでも5社ぐらいが限界だと思います。
私の経験上、基本設計のフェーズが一番重要だと考えています。このフェーズでしっかりとコンセプトと要求仕様を決めておき、関係者の了承をとっておくことがものすごく大事です!
基本設計での決定事項を以降のフェーズで変更すると大きなトラブルが発生したり、大幅なタイムロスが発生します。以降のフェーズでも修正対応は都度発生しますが、コンセプトを大きく変更したりしなければ対応は可能です。
設備導入は、ほぼここで決まるといっても過言ではないのでご注意下さい!
詳細設計
次は実際の設備の導入に向けた詳細設計です。実施設計とも言われます。
このフェーズでは、設備導入に向けた詳細なすり合わせを行っていきます。メーカーとのやり取りの中で最終的にこちらの要求仕様を決定します。見積金額が予算額を大幅に超過している、要求仕様を満たせないなどの懸念があるメーカーは除外することになります。
このフェーズで実施することは以下の通りです。
- メーカーとのすり合わせ
- 生産設備メーカーの選定(2~3社程度)
- 要求仕様の修正・最終決定(DQ)
- メーカーへの詳細見積依頼
- 詳細見積書取得(見積書、見積仕様書)
- 見積書のチェック(要求仕様の抜け漏れ確認)
- 契約書関連確認(工事関連契約の事前確認)
ここで一番重要なのはメーカーの見積仕様書の内容が、こちらの要求仕様をきっちりと満たしていることを確認することです。ここで大きな点を見落とすと後々費用が発生するなど結構ダメージが大きいので要チェックです!
また、設備導入時に必要な工事費用、特に一次側の工事(電気工事など)は見積費用に含まれていないケースが多いです。しっかりと確認しておき、別途費用が発生するか確認しておきましょう!
契約書についても自社の法務部門も交えてメーカーと事前にどういった契約を取り交わすのかを確認しておきましょう!契約書の締結は時間がかかるので、事前に対応を進めておくと今後のやり取りが非常にラクになりますよ。
決済・施工
次に稟議書を起案、決裁~施工のフェーズになります。
メーカーは2~3社に絞っている段階なので、稟議書を起案して金額の交渉の結果、最終1社に決定することになります!その後はいよいよ実物の設備を導入します!
このフェーズで実施することは以下の通りです。
- 稟議起案
- 設備導入メーカー決定
- メーカーとの詳細打ち合わせ(スケジュール、工事内容など)
- 契約書締結(工事請負など)
- 出荷前検査(FAT)
- 設備搬入
- 設備据付(IQ)
設備導入メーカー決定まで行くと、担当者の負担はだいぶ少なくなります。出荷前検査までは少し余裕ができますので、その間にメーカーと導入工事の段取り・スケジュールの調整を行います。その後、メーカーに設備導入・据付まで実施してもらって完了となります。
お断りすることになった他のメーカーにも可能であれば連絡しておく方がいいかと思います。あまり気が乗るものではないですが、今後別の機会でお願いする可能性もありますし、これまでの御礼も込めて連絡しておくのがベターです!
検収・稼働
導入された設備について試運転を実施し、性能上問題無いことを確認できれば、検収→稼働という流れになります。
このフェーズで実施することは以下の通りです。
- 試運転(メーカー側)(OQ)
- 試運転(こちら側)(PQ)
- 検収(立ち合い、完成図書確認)
- バリデーション(プロセス、洗浄)
- 稼働
特に新規導入の場合は、設備の試運転で不具合は間違いなく発生すると思っていた方がよいです。想定の性能が出ないとか、制御プログラムがフリーズしたとか普通に発生します!
稼働予定日の2ヶ月前から試運転、1ヶ月前に検収ができるようにスケジュールを組んでおく方がベターです!くれぐれもギリギリのスケジュールは組まないようにして、不具合に対応できる余裕をもつように心掛けて下さい。
追加の工事や費用の発生する場合もありますのでこの点も要注意です!
バリデーション
最後に設備のバリデーションについて簡単に説明させていただきます。
バリデーションは医薬GMPの概念です。バリデーションとは、「妥当性を検証すること」という意味です。導入した設備が製造に使用する上で妥当であるか、期待される品質を担保でするかを検証する作業となります。
以下の通り、設備の適格性評価を実施後にバリデーションという流れになります。
①適格性評価(クオリフィケーション)
- DQ(Design Qualification:設計時適格性評価)
- IQ(Installation Qualification:設備据付時適格性評価)
- OQ(Operational Qualification:運転時適格性評価)
- PQ(Performance Qualification:性能適格性評価)
①設計時、②据付時、③運転時、④性能確認の4つの点に関して適格であることを証明するための文書を記録として残す必要があります。
②バリデーション
設備の適格性に問題無ければ、以下のバリデーションを行います。
- プロセスバリデーション(Process Validaiton):該当設備も含めて一連のプロセスの中で品質に問題ない製品が製造できるかを検証する。
- 洗浄バリデーション(Cleaning Validaiton):該当設備の洗浄方法が妥当であるか検証する。
こちらも当然ながら実施した記録を文書として残す必要があります。
今の時点では、①適格性評価→②バリデーションを上記の流れでする必要があるということを頭にいれておいていただければよいと思います。
バリデーションは医薬品製造の概念ですので、医薬品以外、例えば、食品製造の設備については必要とならない場合が多いのでその点はご留意下さい。
まとめ
今回は、設備導入の基本の流れについて説明させていただきました。
思っていた以上に記事のボリュームが多くなってしましましたが、最後までお付き合いいただきありがとうございました。
この中でも、特に基本設計時のコンセプトの重要さについて記載させていただきました。コンセプトは、外部環境、内部環境の変化によってすぐにブレてしまいがちになります。上司の意向や会社の意向によっても左右されてしまいがちになるので要注意です。
ここでしっかりとしたコンセプトとそれを落とし込んだ要求仕様を作ること、それを一貫性をもって最後までやり抜くこと、これができれば設備導入は成功すると思います。
ただ、設備導入をすることで周りからの100%の評価は得られません。良くなったという人もいるし、そうでない人もいますのでそこは気にしないようにして下さい。これは立場立場によって考えが異なるので仕方のないことです。
ご参考下さい。
コメント